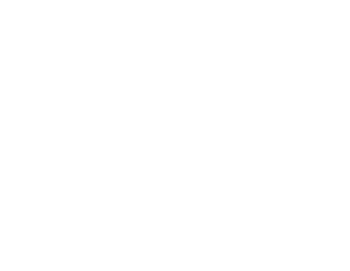
Science, Research & Development
- Sputtering: PVD, HiPIMS, CVD;
- Chemical treatments: Electropolishing, etching, deposition, plasma treatments, cleaning;
- Materials, Surface analysis.
During the long period of any metal product usage, its reliability and other properties gradually deteriorate: it loses its appearance, the part undergoes corrosion, rusts, becomes less strong. It is no longer able to continue to perform its functions to the fullest extent. With a help of (electro)-chemical polishing, it is possible to restore the previous appearance and prolong usage.
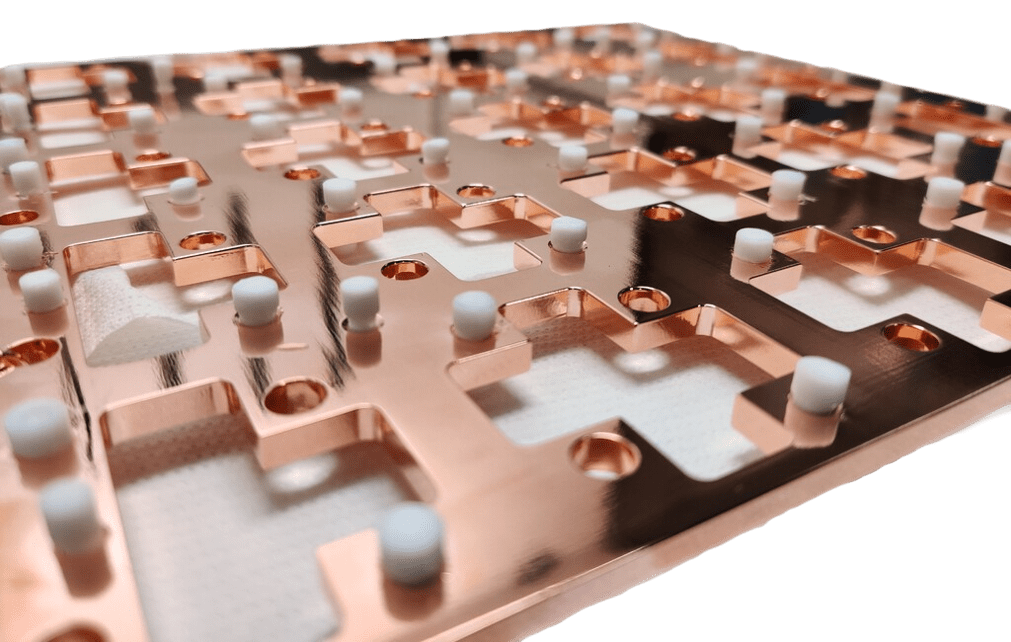
Electropolishing is the anodic treatment of metal parts to give them a shiny appearance and also to smooth small scratches or chips from their surface. It favourably affects the physical, chemical and aesthetic properties of the surface of each metal object. Long electropolishing can as well remove surface contaminations and remove damaged upper layers (from production or mechanical polishing steps).
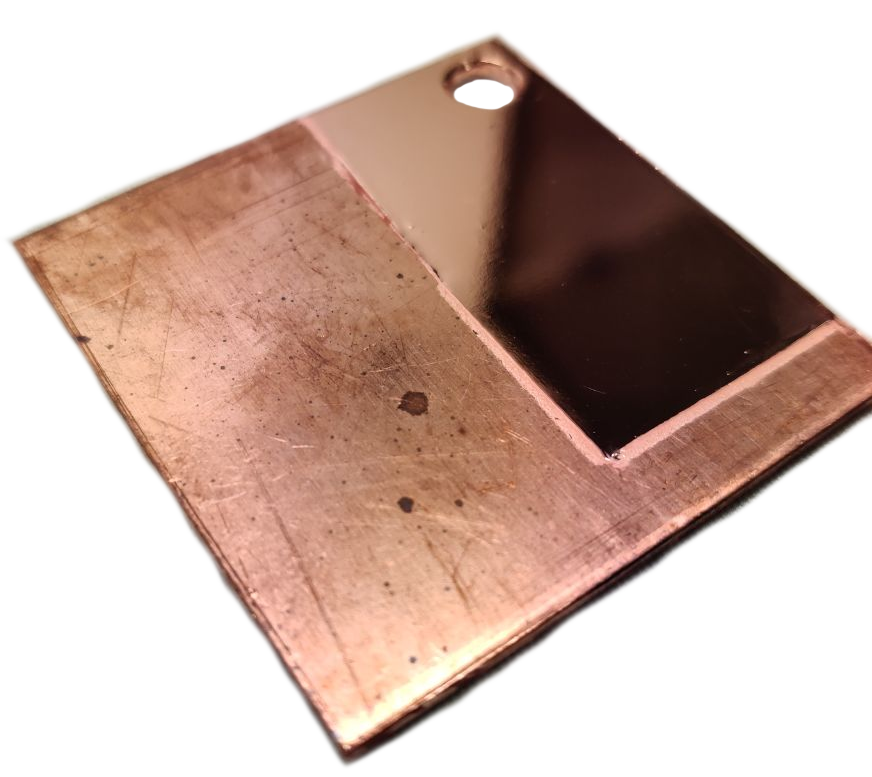
Benefits of doing Electropolishing:
- Improved Corrosion Resistance — Electropolishing is able to remove surface contaminations, that can lead to a local moisturing and as a result – corrosion;
- Required Surface Finish for future deposition (PVD) — EP is a highly demanded process for both chemical and physical deposition processes;
- Ultracleaning — Electropolishing offers ultracleaning capabilities.
- Deburring — electropolishing is an effective process for deburring metal parts. ;
- Enhanced Mechanical Properties;
- Versatility – Works for all metals and its alloys;
We have mastered commonly known and developed our protocols of various metals polishing, i.e. Cu and its alloys, S.S., mild-steel, Al and its alloys, Nb and Ti. Our experience was connected with fundamental researches (such as EP of superconductive radiofrequency cavities) and with Industrial collaborations (to be added.). At our disposal there are two chemical plants, a number of power supplies, including pulse-reverse one and highly powered 500V-90A bidirectional PS. Our goal is a constant improvement of the process with the application of innovative methods, such as pulse and pulse-reverse electroprocessing, ionic liquids electropolishing, plasma electrolytic polishing.
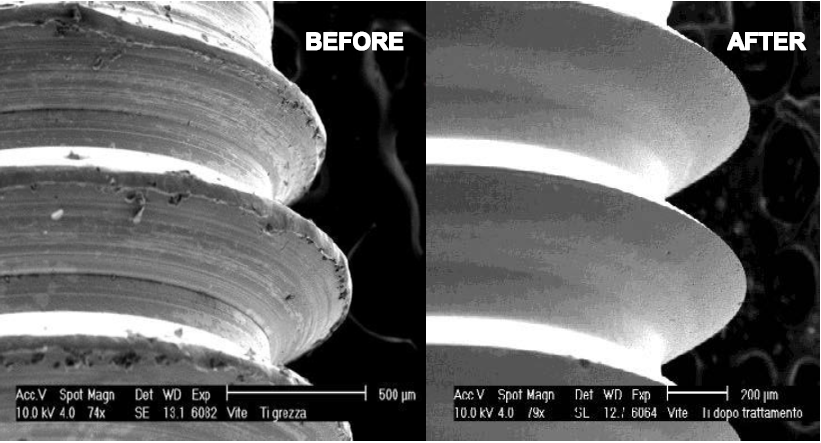
References:
[1] Turley and Samuels; J Iron and Steel Inst, 186 (1957) 211.
[2] P.A. Jacquet, Metal Finishing 47 (5) (1949) 48.