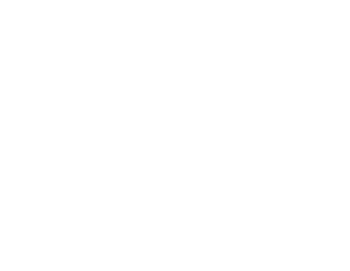
Science, Research & Development
- Sputtering: PVD, HiPIMS, CVD;
- Chemical treatments: Electropolishing, etching, deposition, plasma treatments, cleaning;
- Materials, Surface analysis.
An advanced technique, Plasma Electrolytic Polishing (PEP), that has brought many attention recently both from the industry and scienfitic fields, has all the possibilities to substitute classical electropolishing. A list of advantages makes PEP an ideal candidate for a future “green deal” for the non-destructive surface treatments. High current and high voltage powersupplies are the neccery tool to ignite the process.
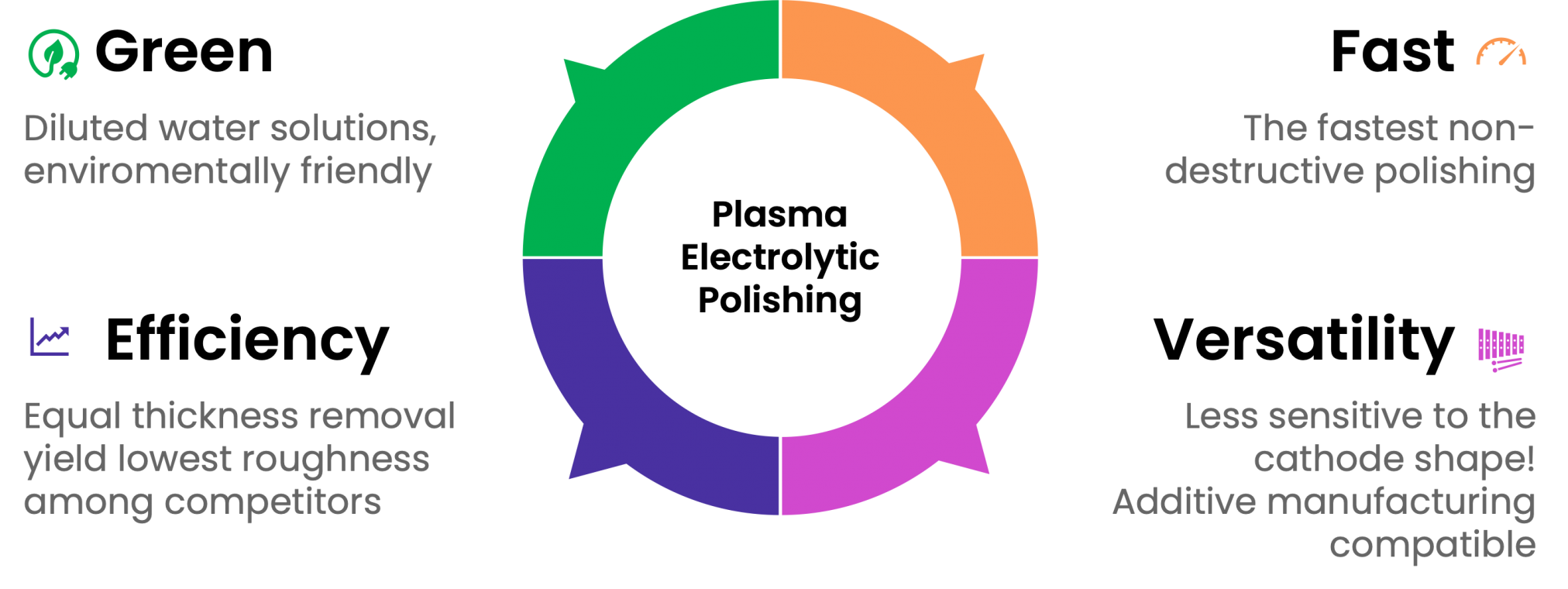
- Green, sustainable (uses diluted water solutions)
- Fastest industry polishing rates (up to 30 um/min)
- Efficient polishing (removing equal thickness, PEP yields to a lower roughness and higher reflectivity among competitors)
- Versatile (cathode geometry is not critical for a process; in principle all metalls and alloys can be polished)
The mechanism remain to be unclear, although, scientist are agreed on the fact that plasma ignition is taking place during PEP. That is possible, due to the formation of the Vapour-Gas Layer (VGL) thin film, that surrounds the sample’s surface. Electrochemical gas production and Joule’s heating of the solutions are the cause of the VGL formation. All the theories are based on the either electrochemical only, or physical only or combinational nature of phenomena.
Various fields application has already begun due to the easiness of industrialisation. The majour applications are:
- Medical;
- Aerospace;
- Precision instruments and tools;
- Industrial manufacturing tools;
- Additive manufacturing.
Surface Technologies and Supercondutivity Service is a frontier leader for the R&D and application of PEP in Italy. 4 original solution composition has been developed and currently undergo patent processing in Italy/EU/world. Copper and its alloys, Stainless steel, Niobium, Tantalium, Aluminium, Silver and its alloys are the metals we have already succeed to work with.